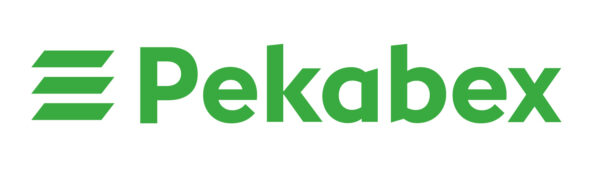
„Mamy do powiedzenia dużo więcej, niż tylko produkcja i budowanie” – mówi Robert Jędrzejowski, prezes Pekabex S.A. …
Po otwarciu w Gdańsku najnowocześniejszej w Europie fabryki elementów żelbetowych typu „filigran”. Oraz ogłoszeniu pierwszego polskiego systemu mieszkaniowego, teraz wraz z inżynierskim start-upem ReBuild wchodzi w temat konstrukcji maszyn. W czasie pandemii COVID-19 kolejnym krokiem do innowacji technologicznych stała się zautomatyzowana linia do szycia maseczek.
Pekabex to lider rynku prefabrykacji, posiadający pięć fabryk w Polsce i setki pracowników na budowach w kraju i za granicą. Z kolei zespół start-upowców tworzą młodzi inżynierowie – studenci i absolwenci związani z Politechniką Warszawską.
Po ogłoszeniu pandemii COVID-19 pojawiła się pilna potrzeba zaopatrzenia w środki ochrony osobistej. Nie tylko własnych pracowników, ale też przedstawicieli służb medycznych, jak również wszystkich osób wychodzących z domu w trakcie trwającej pandemii. To zainspirowało do współpracy dwie firmy z branży zupełnie nie związanej z produktami BHP.
„Na rynku polskim i europejskim brakowało maseczek, a tymi sprowadzanymi – od razu charytatywnie dzieliliśmy się ze szpitalami. Ten brak wprawił nas w zakłopotanie i sprawił, że szukaliśmy nowych rozwiązań. Doskonale znamy możliwości młodych inżynierów z Politechniki Warszawskiej i wiemy, że potrafią tworzyć takie wynalazki. Pekabex dążąc do pozycji lidera innowacji w Polsce i Europie tworzy struktury: poszukuje zdolnych inżynierów i wspiera ich w rozwoju. W tym przypadku zapłaciliśmy za maszynę do tworzenia maseczek, gdyż naszym celem jest produkcja w niskich kosztach. Jednak na pewno nie będzie to nowa linia biznesu Pekabex” – mówi Robert Jędrzejowski.
Prace nad skonstruowaniem nowej maszyny nie zostały porzucone przez firmę nawet pomimo pojawiających się latem sygnałów o słabnących symptomach pandemii. Teraz jest gotowa, by przekazywać maseczki głównie własnym pracownikom i ich rodzinom, a także organizacjom, które lokalnie wspiera i z którymi współpracuje.
Na czym polega zautomatyzowana linia do szycia maseczek?
„Standardowo włóknina jest sprzedawana w belkach 1,6m i długości 1000m. Proces jest ciągły i wykorzystywany jest cały materiał – dzięki temu nie tworzymy odpadów. Maseczki są trochę w stylu IKEA – samodzielnie dodajemy sznureczki do wiązania” – mówi Witold Rządkowski z ReBuild. – „Z uwagi na fakt, że trudno teraz o dostawy czy wykonanie części frezowanych czy toczonych korzystamy z druku 3D. Naszym sąsiadem jest polski producent filamentu HMF Chemical, który drukuje nam te części za darmo i od ręki. Drukujemy z nowego rodzaju tworzywa, opracowanego od podstaw w Polsce – Calibramu. Udało nam się zastąpić części metalowe wykonanymi z tworzywa – nawet tak odpowiedzialne jak mocowanie okrągłych noży, czy takie, które należy jeszcze przebadać pod względem funkcjonalnym, jak rolki do zagniatania maseczek. Cała linia od momentu zapytania powstała w 1,5 miesiąca, a limitujące było tylko wykonawstwo – niektóre części musiały być specjalnie stworzone z metalu”.